Galvanic Cathodic Protection
Zinc is less noble than steel. Basically it means that zinc has a more electronegative potential than reinforcement steel. Hence when zinc is electrically connected to reinforcement the zinc is forced to become the anode and the steel reinforcement the cathode. Current will flow from anode to cathode inhibiting reinforcement corrosion subsequently avoiding concrete cracking and spalling.
Over the last 50 years Impressed Current Cathodic Protection (ICCP) have been found to be suitable for a wide range of concrete structures but the RTA in BSW reports the relatively high cost of ICCP and the high demand on internal resources limits the number of ICCP systems that can be commissioned. Low cost simple galvanic anode CP systems would be an ideal substitute but until recently the systems available have not provided the current density necessary to polarise corroding reinforcement to give corrosion protection.
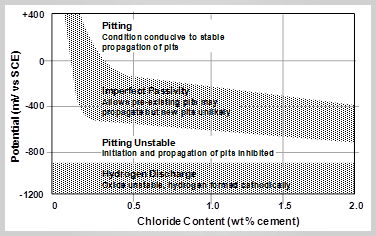
Small anodes giving low anode :cathode area ratios have been shown to be excellent for cathodic prevention as the polarisation required to achieve protection is low. This has now changed with Zinc Layer Anodes, Roll Anodes and Super Anodes all providing the current density, and hence polarisation necessary such that conventional corrosion protection criteria can be applied.
Cathodic Protection, Cathodic Prevention and Incipient Anode Protection
The difference between cathodic protection and cathodic prevention is described by Page in relation to his simplification of Betolini et al’s domains of electrochemical behavior of steel in concrete in the figure above.
From this figure three types of corrosion protection can be identified:
a) Cathodic Protection: For repair of structures corroding due to chloride ingress the reinforcement the reinforcement is polarized from ‘Pitting’ to ‘Pitting Unstable’ to provides protection. This can be a very large shift in potential and a high current demand. A small potential shift to ‘Imperfect Passivity’ reduces the corrosion rate but it may not be sufficient. Anodes that can polarise reinforcement generally need to be based on a uniform current distribution and high anode:cathode anode ratio, e.g. ZLA
b) Cathodic Prevention: In new structures where chlorides have not caused corrosion activation only a small polarization is required to put the reinforcement in the ‘Imperfect Passivity’ domain. If corrosion pits have not formed then even small potential shifts into the zone of imperfect passivity increase the level of chloride necessary to cause corrosion such that corrosion becomes unlikely. Hence cathodic prevention can be achieved by relatively small anodes that give a relatively low current density.
c) Incipient Anode Prevention: The area around a repair is likely to have some chloride but pitting will not have commenced as reinforcement in the repaired area previously acted as the anode so pitting corrosion has not commenced. Such areas can still be protected by a small shift in potential to the imperfect passivity zone.
This basic understanding of corrosion protection is useful when considering the objectives of different galvanic anode systems. Key aspects are:
1) A major benefit of using galvanic anodes such as zinc is that they cannot polarize the steel sufficiently to take it to the hydrogen discharge range.
2) In cathodic prevention systems only a small polarisation is required to insure the steel stays protected while in a corrosion protection higher polarisation is required. A system that is suited to cathodic prevention may not be suitable for cathodic protection.
Other factors in galvanic anode system design are:
1) Current drawn, and hence rate of use of anode, to protect steel in concrete depends on the potential drop, i.e. polarization achieved (current = potential drop x resistance). Hence polarisation achievable depend on the current output from the anode system which is a function of the anode area and current density at the anode.
2) Resistivity if the protection current delivered is proportional to the resistance of the circuit clearly the resistivity of the electrolyte must be considered. In a corrosion cell the spread of the potential field, and hence current can be estimated from the geometry of the anode and cathode, the potential difference and the resistance of the electrolyte at the anode and cathode.
3) Anodes protect the steel reinforcement as they have a lower natural potential than the steel and hence a potential difference is set up between the anode and steel such that the anodes corrodes rather than the steel. Zinc is often used as the anode as it has a small manageable corrosion expansion.
There are many factors that influence a CP system design. SRCP consultants can provide this support and provide a range of anodes.
SRCP anodes available:
Zinc Layer Anodes (ZLA), Roll Anodes, and GSC Super Anodes give lower cost true cathodic protection systems for concrete that can be used:
- where electrical systems are unavailable (e.g. projects with many isolated areas)
- where impressed current systems are uneconomic (e.g. small areas)
- on projects where electrical systems are not suitable (e.g. hazardous area)
- in areas where wiring is not practical (e.g. many mine site areas)
- where localized protection is required (e.g. at corners, joints or areas of localized low cover)
- where incipient anodes may commence active corrosion
The anodes are designed around anode paste that was developed after several years of research. It enable a high current density, produces reactions that do not lead to breakdown, prevents passivation.
CorrPRE’s High Output Galvanic Anodes Revolutionise Reinforcement Corrosion Repair
-
No need to break out sound but contaminated concrete
-
Major saving in breakout cost and effort
-
Noise reduction as no hard breakout
-
Risk of structural failure reduced as reinforcement not debonded
-
Less risk of vibration damage to setting mortar in surrounding repairs
-
Contract period and cost reduced as less hard work to do
Full cathodic protection by galvanic action at patch and surrounding areas
-
no wiring or control systems
-
no monitoring required
-
Simply installed, no CP expertise required
Further Reading
- Relationship between current and corrosion control technical note
- Spreadsheet for assessing design life of galvanic anodes
- “Galvanic Cathodic Protection System Complying with Code Based Protection Criteria” – Paper by F. Papworth & Roberto Giorgini
- “Cathodic Prevention of Steel in Concrete” presentation by Roberto Giorgini
- “Galvanic Anodes for Prevention & Protection of Concrete” presentation by Frank Papworth